Airbus and CFM International to test new open fan engine on an A380
At the Farnborough International Airshow, aerospace manufacturer Airbus and CFM International announced last week a bilateral cooperation agreement to conduct the flight test campaign of a new open fan engine (propfan) developed by the joint venture of General Electric and Safran Aircraft Engines.
The main objective of the project is to accelerate the development of new propulsion technologies with associated lower greenhouse gas emissions. The Flight Test Demonstrator, part of CFM International’s Revolutionary Innovation for Sustainable Engine (RISE) project, will be conducted using a specially configured and instrumented Airbus A380 aircraft.
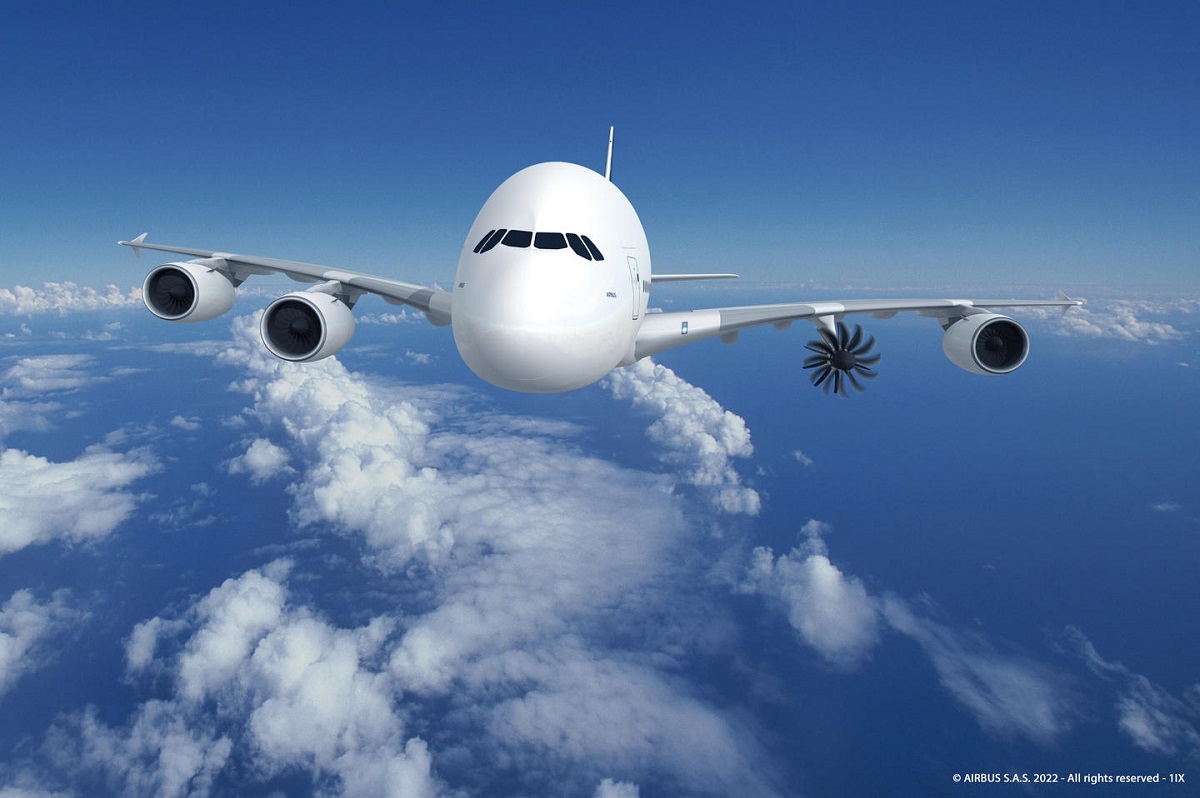
Through the programme, possible future improvements in engine’s performance and efficiency will be studied. The tests will assess the aerodynamic performance of the integration between the engines and the wings, as well as provide data to improve the efficiency of the propulsion systems.
Both Airbus and CFM International said the new solution would reduce carbon dioxide emissions by up to 20% «compared to today’s most efficient engines» when using traditional Jet-A fuel. Furthermore, the reduction would be even greater when using sustainable aviation fuel (SAF). In this respect, the programme will assess the compatibility of the technology with new sustainable fuels.
«New propulsion technologies will play an important role in achieving aviation’s net-zero objectives, along with new aircraft designs and sustainable energy sources», said Sabine Klauke, Airbus Chief Technical Officer.
The first open rotor engines are scheduled to enter service in the mid-2030s.
Still a long way to go
The Airbus A380 equipped with the new propulsion technology will operate from the European manufacturer’s facility in Toulouse, France. According to information from both companies, the first demonstration flight is expected to take place in the second half of this decade. Before that, however, an intensive phase of routine ground testing must be completed. It will be carried out at GE Aviation’s facility in Victorville, California.
«We will first need to determine the flight physics constraints, design and assessments for the flight-test demonstration engine installation», said Pascal Arrouy, Airbus’ Open Fan Architect. He added that the work will include «assessment of loads, handling qualities and performance, and preparation of modeling to support flight-test analysis».
Together, the two companies will design the engine-to-wing attachment system, with the aim of minimising weight and vibration transmission. The performance of the affected fuselage structure will also be studied and various aircraft systems will be modified to ensure the desired behaviour during testing and to support the validity of the data obtained.
Once these activities are completed, the project will move on to the next phase: the physical manufacture of the engine and the assembly of the necessary modifications to the aircraft. This will be followed by specific tests on the engine components. The interior of the aircraft will be set up with workstations for engineers and technicians to analyse the in-flight performance. As with such tests, the Airbus A380 will be instrumented with hundreds of sensors, microphones, static pressure sensors, accelerometers and cameras.
See also: Airbus and seven airlines sign LOI’s to explore CO2 capture solutions
Para comentar, debés estar registradoPor favor, iniciá sesión